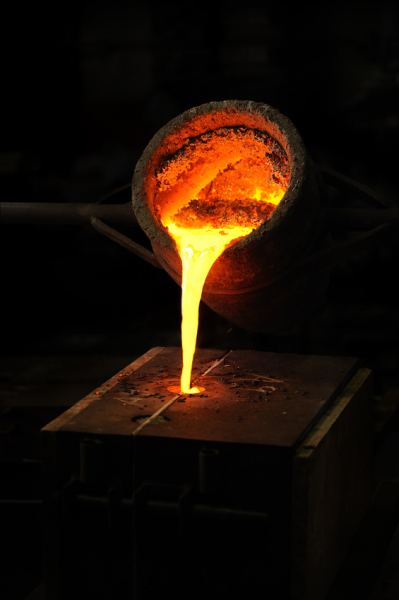
We have both metal forging and metal casting capabilities.
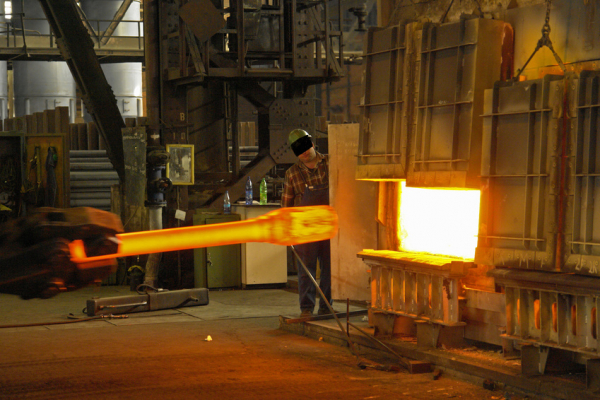
Sun Fast provides offshore sourcing for metal forging.
Metal Forging vs. Metal Casting
Offshore metal forging and metal casting are two processes that are commonly managed by international outsourcing companies when a business is unable to handle all aspects of a specific project. This can include finding skilled labor, access to specialized equipment and securing quality materials at a more affordable cost.
Using offshore metal casting services provides a range of benefits for companies. One primary benefit is lower labor and raw material costs, which allows you to meet production demands while keeping expenses low. Companies that use an outsource manufacturing service for offshore metal forging also benefit from fewer operational concerns related to staffing and equipment maintenance and can expand their capabilities without having to purchase new equipment or a larger facility.
When you don’t have to worry about these and other day-to-day tasks, you can place more focus on strengthening and building your business. Learn more about our offshore metal forging and metal casting services or contact us to discuss your project.
Globally Sourced Metal Forging & Metal Casting Experts
Sun Fast International has numerous metal casting and metal forging offshore sourcing capabilities. We also offer comprehensive, turnkey project management to coordinate every aspect of the offshore manufacturing process. From design and prototyping to full production, packaging, and shipping, we have the connections and contacts to provide offshore sourcing and fabrication services for a wide range of products.
Our international outsourcing solutions provide you with access to skilled workers and specialized suppliers to deliver the quality, expertise, and flexibility you need to get the job done right the first time. All our offshore metal casting and manufacturing facilities are regularly screened and audited to ensure that they meet our high standards of quality. We select the facility that is best suited to the manufacturing requirements of your product to give you the most efficient and most cost-effective option for your project.
Metal Casting and Metal Forging Methods
Metal forging and metal casting are the two most reliable and versatile methods for manufacturing metal parts and components for industrial, or heavy-duty applications. In many cases, the same part could be created using either metal casting or metal forging with roughly equal results. However, the two cannot be interchanged without significant revisions to part designs. Additionally, pricing can vary greatly from project to project; neither process will consistently be the more affordable option.
So, which method is better for your specific needs? Are there advantages to using offshore metal forging vs. casting, or vice versa?
Sun Fast International provides services for metal castings, steel forgings and aluminum forgings and can also offer unique insights into all three processes. Our experts will help you determine which method will work the best for your project requirement needs and find the right outsource manufacturing solution for your project.
What are Custom Metal Castings?
Metal casting occurs when molten metal is poured or injected into a custom-made mold. After the metal cools and hardens the finalized metal part shape is then ready to be finished. This can be accomplished through additional machining and other processing techniques that are used to achieve desired tolerances and finishes.
There are several different methods that are available for casting apart. The most popular methods include die, sand, and investment casting. Each method uses a slightly different process but delivers the same results. The casting method used depends on the metal or alloy being cast, and the dimensions and geometry of the part design, among other factors.
Because molten metal flows much like a liquid and can completely fill all areas of an intricate mold shape, metal casting is the preferred process for creating complex metal parts. Metal casting is also far better suited for making parts that require internal cavities. There is essentially no upper or lower size limit for cast parts, making it the ideal method for small to very large parts.
Contact Sun Fast today for your offshore metal casting needs, or request a quote today.
Metal Casting Advantages
Metal casting provides several distinct industrial advantages, some of which include:
- Accepts higher tolerances for more detailed part designs
- Creates closer to net-shape parts that require less secondary machining/processing
- Nearly always lighter than otherwise-identical forged parts
- Easier and less time-consuming modification of part designs and accompanying molds
Metal Casting Disadvantages
Metal casting is not always the preferred method for creating parts, some of the disadvantages include:
- Often exhibit more surface porosity than forged parts and may contain unintentional voids
- Not as tough as forged parts (cannot withstand as much pressure or frequency of impact)
- Requires more operator monitoring and interaction to maintain quality and prevent defects
What are Custom Metal Forgings?
When creating custom steel forgings or aluminum forgings, massive compressive forces are used to shape a solid piece of metal into its desired shape. The raw metal is forced under thousands of pounds of pressure into a die that gives the part its shape (similar to a mold used for casting). In addition, post-forging parts often require a good deal of additional machining or other processing to reach the desired final shape, dimensions, or finish.
There are several different classifications of forging that can be used. The choice is based on process temperatures (hot or cold forging) and the type of die utilized (open- or closed-die forging). The forging method used depends on the metal or alloy being worked, and the application(s) for which the parts will be used.
The high pressure that is used within the steel forgings or aluminum forgings process causes metallurgical recrystallization and grain refinement, which conforms to the shape of the part. This results in mechanically stronger parts with greater impact strength, shear strength, and wear resistance.
Contact Sun Fast today for your turnkey offshore metal forging needs, or request a quote today.
Metal Forging Advantages
Metal forging provides several distinct industrial advantages, some of which include:
- Better structural integrity and increased mechanical strength due to the altered grain structure
- Cost savings due to less material scrap and reduced labor requirements
- Forging process eliminates surface porosity, cavities/voids, and discontinuities
- Greater reliability and consistency in ductility, known yields, and increased strength
Metal Forging Disadvantages
Metal forging is not always the preferred method for creating parts, some of the disadvantages include:
- Tight tolerances are difficult to acquire due to the nature of the process
- Numerous secondary processes may be required to meet final design specifications
- Forging process limits the intricacy of shapes that can be produced
Learn More About Sourcing Metal Casting Services from Sun Fast International
Which process is right for your application: metal forging or metal casting? Submit your project to Sun Fast International for a complimentary price quote detailing both options, or contact us for more information.